1997년 이후 4차에 걸친 증설로 87만여㎡ 규모로 확장UHP생산량이 56%에 달하는 한국타이어 핵심 생산기지
이 같은 한국타이어의 성장 발판으로 세계 최대 타이어 공장으로 꼽히는 금산공장의 역할을 빼놓을 수 없다.
14일 한국타이어 글로벌 생산기지인 금산공장을 찾았다. 1997년에 완공된 금산공장은 대전공장에 이은 한국타이어의 두 번째 공장이다.
1997년 설립 이래 현재까지 4차에 걸친 증설과 확장을 마친 금산공장에는 총 1조원 이상이 투자됐다.
이에 따라 87만2000㎡(약 26만4000평) 규모로 확장되면서 ‘세계 최대 타이어 공장’이라는 수식어가 붙어 있을 정도로 엄청난 규모를 자랑했다.
금산공장은 1~4공장으로 구성돼 있다. 제1공장에서는 승용차용 타이어(PCR) 라인과 초고성능 타이어(UHP) 1라인이 돌아간다.
제2공장은 트럭&버스용 타이어(TBR) 라인과 UHP 2라인으로 구성됐다. 제3공장은 UHP 3라인, 제4공장은 TBR 2라인이 들어가 있다.
이날은 제3공장을 둘러봤다. 금산공장은 한국타이어 기술력의 척도가 되고 있는 UHP 생산의 중심지이기도 하다. 전체 생산량의 56%가량이 UHP이다.
특히 금산 제3공장은 UHP만 집중적으로 생산하고 있는 한국타이어 UHP 생산의 산실이다. 지난해 한국타이어가 글로벌 UHP 매출액 2조1400억원을 달성하는데 혁혁한 공을 세웠다고 할 수 있다.
제3공장은 자동화가 가장 잘 되어 있는 대표적인 시설로 꼽히기도 한다. 하루 1만9500본의 타이어를 생산하고 있음에도 불구하고 전체 직원은 280여명에 불과하다.
4개조가 1일 3교대로 근무하고 있는 것을 감안하면 공장이 돌아가는 동안 상주하는 직원은 70여명에 불과한 셈이다.
이는 무인자동화시스템으로 로봇과 무인차량이 자동으로 돌아다니기 때문에 가능한 일이다. 또한 무인차량은 사람이 지나가면 자동으로 멈추는 등 안전에도 신경을 쓰고 있다.
이날 살펴본 공정은 ‘재단공정→성형공정→가류공정→검사공정’으로 이어지는 과정이다. 흔히 타이어를 고무를 깎아 만드는 것으로 오해하기 쉬운데 사실은 고무를 조립해 만든다고 할 수 있다.
먼저 재단공정은 천연고무를 압연해 만들어진 고무판을 정해진 틀과 각도에 따라 재단하는 공정이다. 얇은 고무판을 틀에 맞게 자르는 과정으로이라고 요약할 수 있다.
재단된 타이어를 생산하기 위한 반제품이 된다. 성형공정은 반제품을 모아서 조립하는 과정이다.
성형기에는 2개의 드럼이 돌아가고 있었다. 각각의 드럼은 타이어의 바깥과 안쪽을 각각 조립하고, 두 개의 드럼에서 만들어진 반제품이 합쳐지면서 타이어의 틀을 갖추게 된다.
이렇게 만들어진 타이어를 ‘그린 타이어’라고 부른다. 그린 타이어는 아직 미완성이라는 의미로 가류공정을 거쳐야 완제품이 될 수 있다.
가류공정은 그린 타이어를 몰드에 넣고 일정시간 압력을 가해 가류하는 과정이다. 이는 말랑말랑한 고무의 성질을 딱딱하게 바꿔주기 위한 것이다.
쉽게 말해서 밀가루 반죽을 오븐에 구우면 딱딱한 빵이 나오듯이 타이어를 몰드에 넣고 찌는 것이라고 할 수 있다.
가류공정은 보통 170~180도의 열을 가하기 때문에 곧바로 냉각 과정을 거치게 된다. 가류 시간은 승용차용은 10~12분, 트럭 등 대형차는 40~50분이 걸린다고 한다.
가류공정을 마친 완제품 타이어는 검사공정을 거치게 된다. 먼저 전문 검사관들이 육안으로 체크한 후 기계를 통해 전체적인 균일성 검사를 한다.
마지막으로 엑스레이 검사를 통해 내부 이물질 여부를 검사한다. 이렇게 검사공정을 모두 마친 타이어는 물류창고로 이동해 출고를 기다리게 된다.
한편 공장 내부에는 타이어 특유의 고무 냄새가 가득했다. 이에 대해 한국타이어 측은 천연고무의 냄새로 인체에 무해하다고 강조했다.
강길홍 기자 slize@
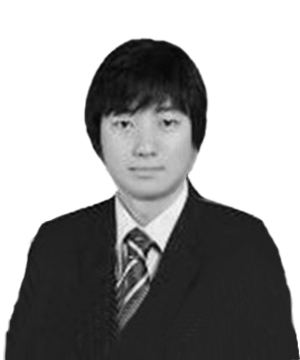
뉴스웨이 강길홍 기자
slize@newsway.co.kr
저작권자 © 온라인 경제미디어 뉴스웨이 · 무단 전재 및 재배포 금지
댓글