평택공장 조립3라인···"전 차종 혼류 생산 가능"자동화 시스템 방식으로 라인 운영 효율 극대화
경쾌한 드릴 소리와 소란스러운 기계음이 가득한 곳. 지난 한 해 총 11만6099대의 자동차를 판매하기 위해 직원들이 밤낮없이 구슬땀을 흘렸던 KG 모빌리티 평택공장을 방문했다.
지난 10월 중순부터 약 2개월간 생산방식이 다른 이종 차종 간 혼류 생산을 위한 2라인과 3라인 통합 공사를 마무리한 KG 모빌리티의 평택공장은 그 어느 때보다 분주했다.
기존에는 1라인과 2라인에서 티볼리·티볼리 에어, 코란도, 토레스 등 모노코크(자동차 뼈대와 보디가 하나로 돼 있는 차량 구조) 차종을 생산하고 3라인에서 렉스턴과 렉스턴 스포츠&칸 등 바디 온 프레임(강철로 만든 별도의 뼈대에 보디를 올린 차량 구조) 차종을 생산하는 구조였다.
전명 통합 공사 이후 현재는 1라인과 3라인, 2개 생산 라인을 운영하면서 3라인에서 프레임 차종과 모노코크 차종을 모두 생산할 수 있게 됐다. 혼류 라인 운영으로 생산 라인의 유연성을 확보해 운영 효율화를 극대화한 것이다. 공장 생산 능력도 시간당 22대에서 30대로 향상됐다.
박장호 KG 모빌리티 생산본부장은 "KG그룹 편입 이후 신속한 의사결정을 통해 약 500억원을 투자해 전면 통합 공사에 돌입했다"며 "국내에서 바디 온 프레임 차종과 모노코크 전기차 차종을 혼류 생산하는 것은 처음이다"라며 자부심을 드러냈다.
이번에 통합 공사를 마친 조립 3라인은 언뜻 기존 공정과 별 차이가 없어 보였다. 컨베이어벨트를 타고 이동하는 차체에 직원들이 순차적으로 각종 장비와 시트, 엔진과 변속기 모듈을 장착하며 하나의 차를 완성해 나간다.
차이점은 '의장→샤시→파이널' 공정으로 이어지는 과정 중 샤시 공정에서 극명하게 나타난다. 샤시 라인에서는 엔진과 구동장치를 트림바디에 장착하고 원활한 작동·제어를 위한 부품을 조립한다.
이 단계에서 모노코크 차종은 파워트레인 모듈과 차체의 위치를 자동으로 맞춰 하나의 차량으로 합치는 '매리지(Marriage)' 공정을, 바디 온 프레임 차종은 엔진과 내부 장비가 조리된 차에 차체는 씌우는 '바디 마운트(Body Mount)' 공정을 거친다. 차체와 프레임이 하나로 구성된 모노코크 형태에 비하면 다소 복잡한 공정이기도 하다
두 차종은 서로 다른 두 공정을 요구지만 KG 모빌리티는 바디와 데크를 동시 운반하는 자동화 시스템 방식으로 공법을 일원화했다.
정해진 조립3팀 책임매니저는 "새로 만든 샤시라인의 핵심은 바디마운팅으로 동시에 도킹할 수 있도록 설비했다"며 "두 차종은 휠 볼트부터 배터리까지 다양한 부품이 서로 다른데 자동화 설비로 통합 공급 라인을 구축했다"고 설명했다.
실제로 작업이 한창인 생산라인엔 렉스턴 스포츠가 주를 이루는 가운데 중간중간 토레스 EVX가 자리 잡고 있었다. 서로 다른 두 차종이 혼재해 있지만 데크와 차체가 도킹되는 시간은 단 3분 20초. 이마저도 20초는 이동시간이다.
두 차종이 혼재돼 있지만 사실상 생산능력은 이전과 같다는 뜻이다. 오히려 생산라인의 유연성을 확보해 추후 효율을 극대화 할 수 있다.
박장호 생산본부장은 "조립 1라인 모자란 양을 3라인에서 커버하고 있다"며 "현재는 전기차 수요가 많아 토레스EVX를 생산하고 있지만 추후 수요에 따라 다양한 차종을 생산할 계획"이라고 말했다.
이번 혼류 라인의 핵심은 '자동화'다. KG 모빌리티의 자동화 기술력은 차체에 해당하는 공정이 이뤄지는 차체2공장에서 더 확실히 확인할 수 있었다.
수십여명의 직원들이 분주하게 움직이던 조립 공장과 달리 이곳에선 곳곳에 설치된 로봇팔들이 분주하게 움직이고 있었다. 용접자동화률 100%를 자랑하는 차체 공장은모든 용접작업을 로봇이 담당하고 있는 만큼, 그 속도와 정확도에 의심의 여지가 없다.
안종석 차체1팀 책임매니저는 "이 공장에서는 작업자를 마주칠 일이 많이 없다"며 " 높은 자동화유롤 인해 미세 조종이나 품질 등 일부 공정에만 작업자가 배치된다"고 설명했다.
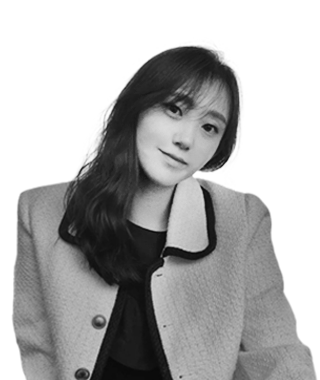
뉴스웨이 김다정 기자
ddang@newsway.co.kr
저작권자 © 온라인 경제미디어 뉴스웨이 · 무단 전재 및 재배포 금지
댓글