마이바흐·S클래스·EQS 만드는 '고급차 생산의 산실'디지털화 혼류 생산으로 품질·생산 유연성 동시 챙겨공장 곳곳에 녹지·태양광 발전 등 친환경 요소도 담아
2020년 9월에 문을 연 이후 친환경 미래형 스마트 팩토리를 지향하고 있는 진델핑겐 '팩토리 56'을 지난 23일 다녀왔다.
메르세데스-벤츠 진델핑겐 공장은 벤츠가 독일에 세운 완성차 조립 공장 중에서 규모가 제일 큰 공장으로 벤츠 완성차 생산의 핵심이자 주력 생산기지 역할을 하고 있다.
진델핑겐 공장의 전체 면적은 264만㎡로 서울 마포구 월드컵공원 면적에 맞먹는 수준이며 세계 최대 규모의 단일 자동차 공장으로 꼽히는 현대자동차 울산공장 면적과 비교하면 대략 절반 규모에 달한다.
전체 공장에서 서쪽 끝에 자리한 팩토리 56은 건물 바닥면적의 합계가 축구장 30개 크기에 맞먹는 22만㎡(약 6만6600평)에 달할 정도로 큰 공장이다. 공장 면적은 크지만 실제로 이 공장에서 일하는 직원은 약 1200명에 불과하다.
이 공장은 메르세데스-벤츠가 지난 2014년부터 추진하고 있는 생산 시설 혁신 프로젝트의 일환으로 세워진 곳으로서 공장 구축에 총액 7억3000만유로(공장 구축 기간 당시 환율 기준 한화 약 1조350억원)가 투입됐다.
이 공장에서는 메르세데스-벤츠의 플래그십 대형 세단 모델인 S클래스와 고급형 브랜드 마이바흐의 차가 생산되고 있으며 고급 전기차 세단인 EQS 등도 생산되고 있다.
팩토리 56에서 가장 돋보였던 특징은 S클래스, 마이바흐, EQS 등이 각자 다른 설비가 아니라 같은 설비에서 혼류 생산되고 있는 점이었다. 혼류(混流) 생산은 한 곳의 생산 설비에서 여러 가지 차종이 섞여서 생산되는 방식을 뜻한다.
통상적으로 대부분의 자동차 회사가 택한 공장 운영 방식은 컨베이어 벨트를 통해 움직이는 소품종 대량 생산 목적의 단일 차종 생산이다. 소품종 대량 생산 방식은 원가 절감 효과가 크지만 제품 생산 성과의 효율성은 떨어진다.
무엇보다 고객의 여러 요구를 반영하기에는 유연성이 떨어지고 천편일률적인 차가 공급되기 때문에 고객의 만족감도 다소 떨어질 수 있다. 아울러 생산 차종 교체에 매우 긴 시간이 걸려 생산량 목표를 맞추기 힘들다는 점도 소품종 대량 생산의 큰 단점 중 하나다.
혼류 생산의 가장 큰 장점은 생산 효율성과 유연성이 높아진다는 점이다. 단 1~2일의 공사만 거치면 손쉽게 생산 차종 변경이 가능하다. 생산 속도는 다소 느릴지언정 고객들이 원하는 차를 자유롭게 생산할 수 있기에 기업의 부가가치는 더 크게 높아질 수 있다.
벤츠 측에서도 이 공장의 최대 장점으로 혼류 생산을 통해 고객에게 최고의 품질을 갖춘 차를 공급할 수 있다는 점을 적극 강조했다.
다만 혼류 생산 체계를 채택한 탓에 단순 생산 속도는 매우 느린 편이다. 이 공장에서는 지난해 말 기준으로 연간 22만대의 차를 생산했다. 공휴일을 제외한 날짜 수를 기준으로 하루 평균 생산량을 환산하면 약 710대 정도의 차가 완성되는 셈이다.
이채로운 것은 구동계 종류가 전혀 다른 내연기관차와 전기차가 같은 설비에서 앞뒤로 번갈아 함께 생산된다는 점이었다. 종류가 전혀 다른 차임에도 오차 없이 차가 만들어질 수 있는 비결은 디지털 전환에 있다.
팩토리 56에는 실시간 디지털 데이터로 승용차 생산 체계를 운영하는 'MO360' 시스템이 적용됐다. MO360을 통해 최적화된 생산 제어를 제공하고 생산 과정에서 각 직원이 활용해야 하는 주요 정보와 작업 지침을 수시로 공유하는데 이 모든 것을 디지털화했다.
이 공장에서는 최종 조립 과정 일부를 제외하고는 대부분 자동화 체제를 택하고 있다. 천장에 걸려있는 인클라인 컨베이어를 통해 차체가 움직이고 바닥의 마그네틱 선을 따라서 공장 내부를 부지런히 오가는 400여대의 무인 트럭(AGV)이 부품을 각 공정 작업장에 운반했다.
모든 설비는 디지털 방식으로 상호 연결돼 있고 5G 통신망을 통해 전 공정의 작업 내용을 디지털 문서에 기록하고 있다. 만에 하나 있을 생산 과정에서 돌발 변수나 오류가 발생해도 실시간 대응이 가능하다.
천장에 걸려있는 차체와 공장 바닥에서 운반되는 엔진 등 동력장치는 '풀 플렉스 메리지'라고 표현된 공정에서 서로 조합된다. 이 과정도 전부 디지털로 진행되는데 최종 조립과 검수 과정만큼은 사람의 손을 거친다.
팩토리 56 관계자는 "대부분 공정의 디지털 전환을 이룬 공장이지만 여전히 사람의 손길이 필요한 부분이 있다"며 "조립 공정의 일부를 사람이 맡는 것은 기계가 할 수 없는 일을 사람이 대신할 수 있기 때문"이라고 말했다.
그는 "이 공장에서 생산되는 차 중에는 고객의 요구에 따라 맞춤 제작된 차들이 있는데 기계 대신 숙련도가 높은 베테랑 근로자들이 이 차의 조립을 맡는다"며 "팩토리 56은 최고의 품질과 높은 생산 유연성이 조화를 이루는 사업장을 추구하고 있다"고 덧붙였다.
실제로 이 공장은 자동화의 물결 속에도 사람의 소중함을 강조하고 있었다. 공장 안팎의 전반적인 분위기는 매우 여유로웠다. 곳곳에 휴게 공간도 충분히 마련돼 있었고 근로자들이 만족스러운 표정으로 업무에 몰입하고 있었다. 이러한 분위기는 벤츠가 근로자들의 여유로운 근로 여건을 보장한 덕분이다.
근로자의 안전함과 편안함을 강조한 부분도 있다. 천장에 걸린 인클라인 컨베이어가 대표적 사례다. 이 기기는 조립 공정 때 근로자가 자신의 체격에 맞게 차체를 이동시킬 수 있다. 근로자들이 최대한 편한 자세에서 일하게끔 하려는 배려의 증거였다.
디지털화된 공정이 대부분인 탓에 팩토리 56의 근로자 신규 채용은 이뤄지지 않고 있다. 그러나 기존 인력의 해고는 전혀 없다. 대신 꾸준한 직무 재교육 과정을 거쳐서 업무를 수행한다. 진델핑겐 지역사회와의 끈끈한 유대 관계 유지도 잊지 않는 부분이다.
팩토리 56의 또 다른 특징은 지속 가능한 탄소 중립형 친환경 공장으로서의 해답을 제시했다는 점이다. 이 공장의 상부 중 40%는 풀과 나무가 심어진 녹지 공간으로 조성돼 있다. 벤츠 측은 이를 '녹색 지붕'이라고 표현했다.
'녹색 지붕'은 공기 중에 섞인 오염 물질을 걸러내 공장 주변 공기 질 개선에 긍정적 영향을 주고 있다. 진델핑겐을 비롯한 슈투트가르트 일대는 자동차 생산 공장이 워낙 많은 탓에 독일에서도 공기 질이 나쁘기로 소문난 지역으로 꼽힌다. 그렇기에 '녹색 지붕'이 매캐한 이 지역의 공기를 정화하는데 큰 역할을 해줄 것으로 기대되고 있다.
녹지 공간이 아닌 지붕 부분에는 태양광 집열판을 설치해서 자체 발전을 하고 있는데 태양광 발전을 통해 얻어진 전력은 팩토리 56에서 쓰이는 전기의 30%를 담당하고 있다.
또 빗물을 저장하고 천천히 환경으로 방출하는 역할을 하는 한편 여름과 겨울에는 자연 단열재의 역할을 해 건물의 열 흡수를 방지하고 냉난방 에너지 소모량을 줄이게 하고 있다.
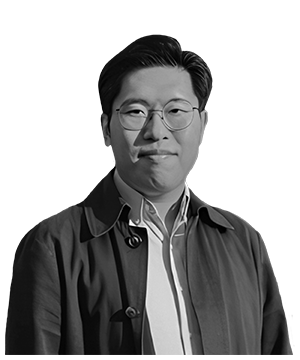
뉴스웨이 정백현 기자
andrew.j@newsway.co.kr
저작권자 © 온라인 경제미디어 뉴스웨이 · 무단 전재 및 재배포 금지
댓글